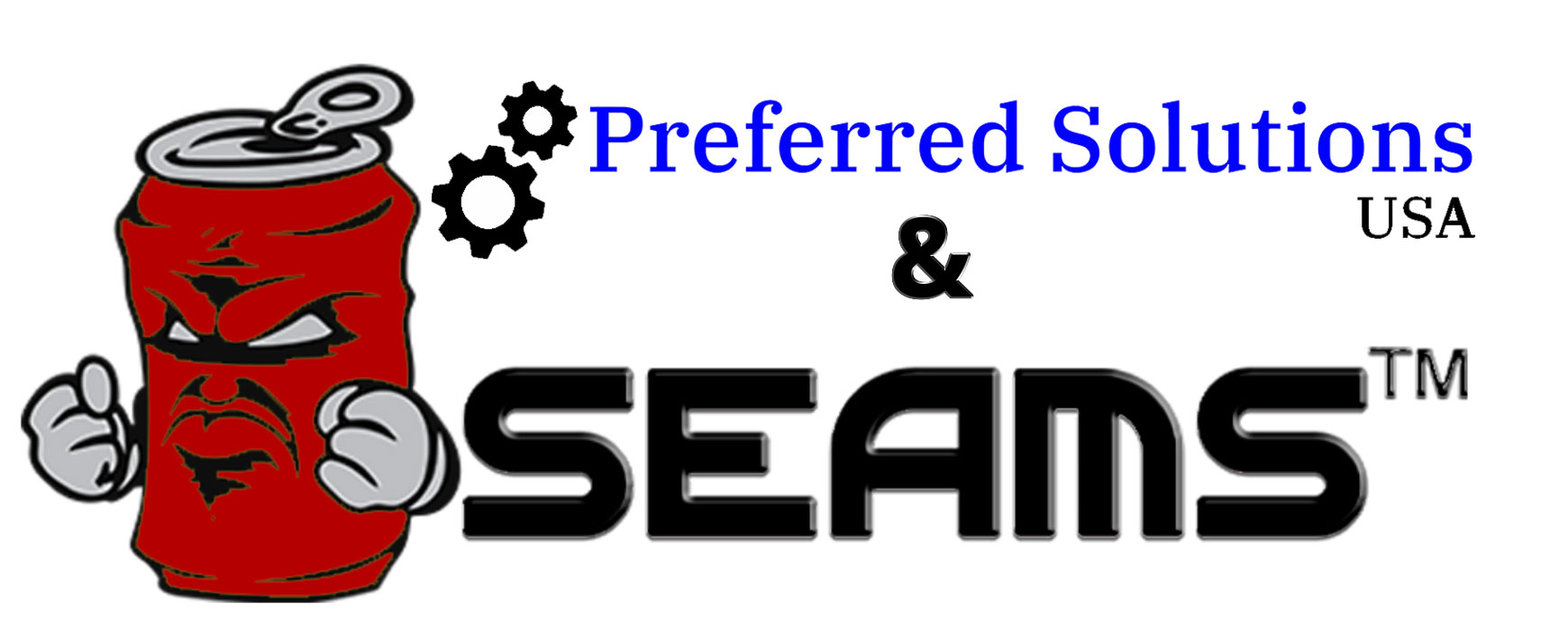
We have channeled 75 years of can, lid, and seamer manufacturing experience into our SEAMS™ program which utilizes statistical analysis of your internal seam data into exception reports. These reports highlight the seam characteristics which may need adjustment based on runs and trends. We then lend our reaction guides and MAP's (Machine Adjustment Procedures) to the maintenance teams to help reenforce the increased knowledge needed to properly make these adjustments. This will significantly reduce quality issues while elevating adjustment knowledge within your facility. We can safely state that no other service provider has this solution.
SEAMS™ 4 Prong Approach
SEAMS™ Evaluation & Monitoring Support
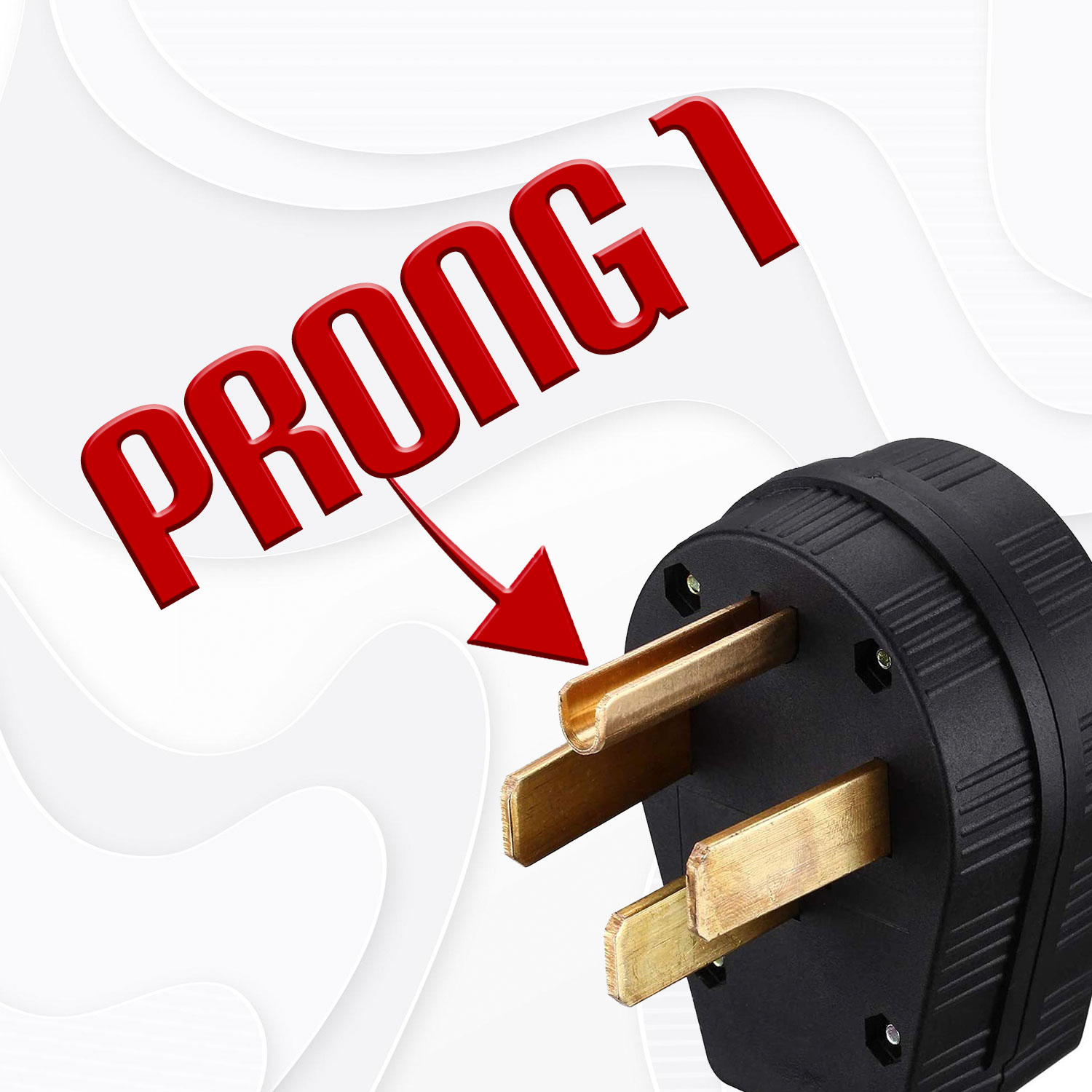
Comprehensive QA and Maintenance Training
This includes seam analysis, reaction guides, and MAP's (Machine Adjustment Procedures)
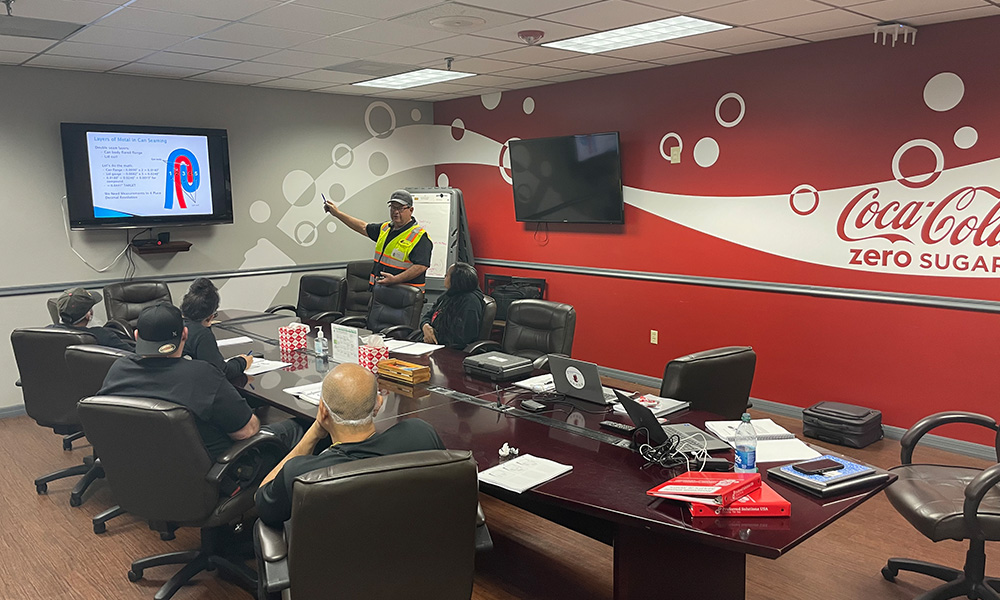
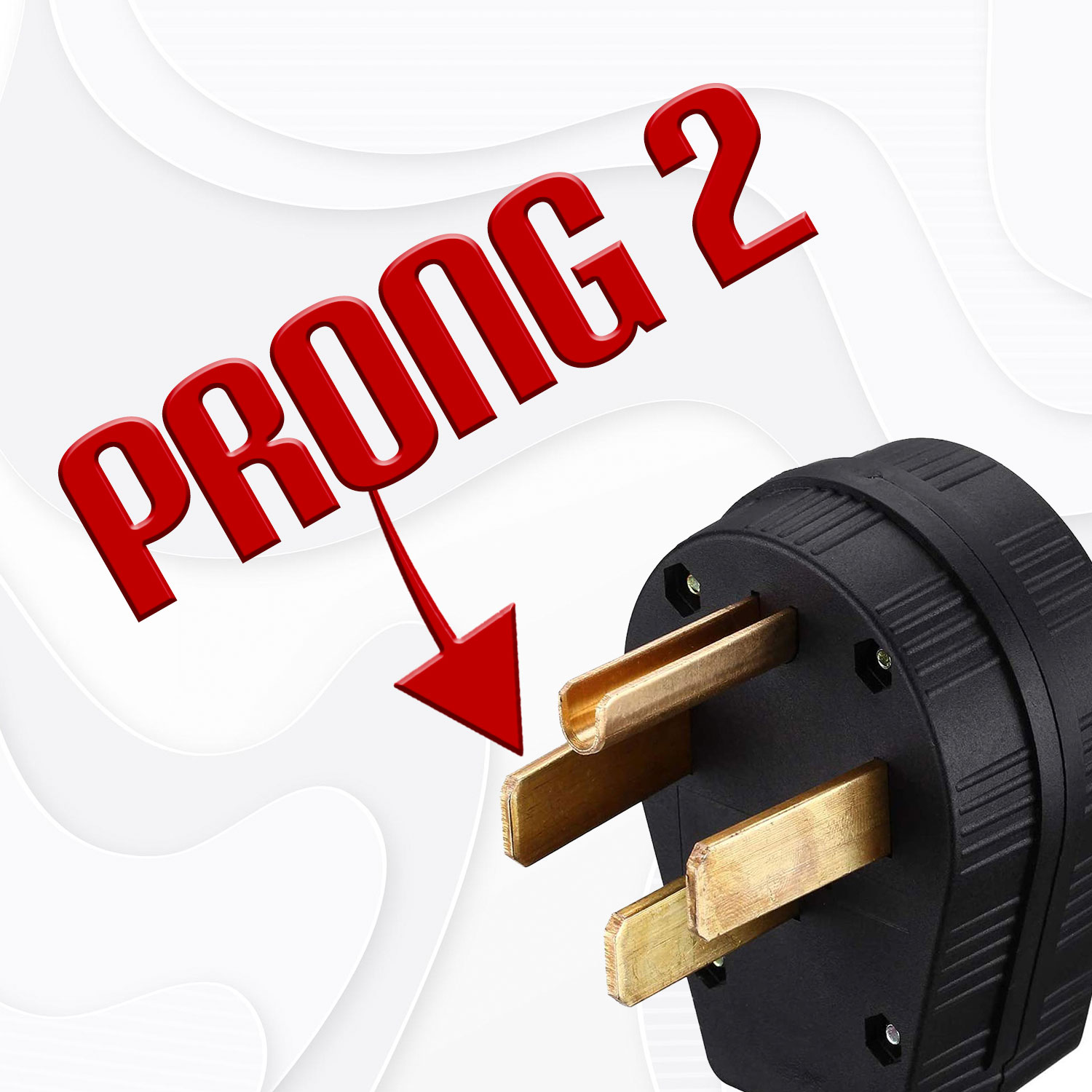
Monthly Line Monitoring
Monthly exception reports outlining the 4 critical characteristics relative to seam integrity which are seam thickness, countersink, seam height, and body hook including cover hook, overlap, seam gap, and tightness characteristics.
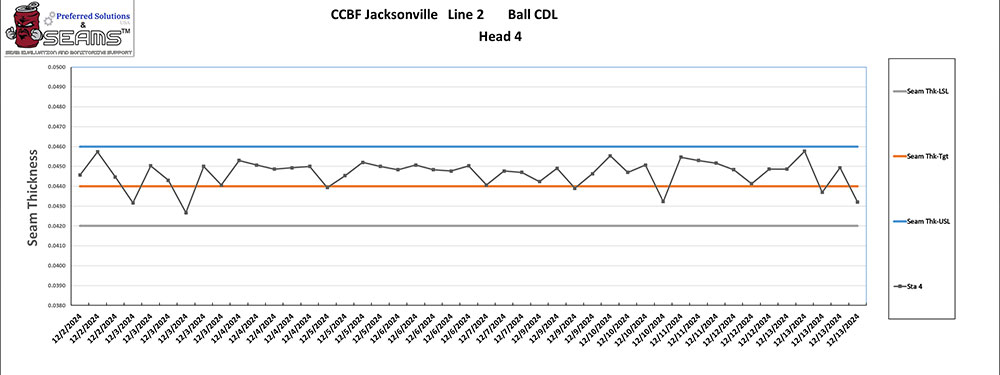
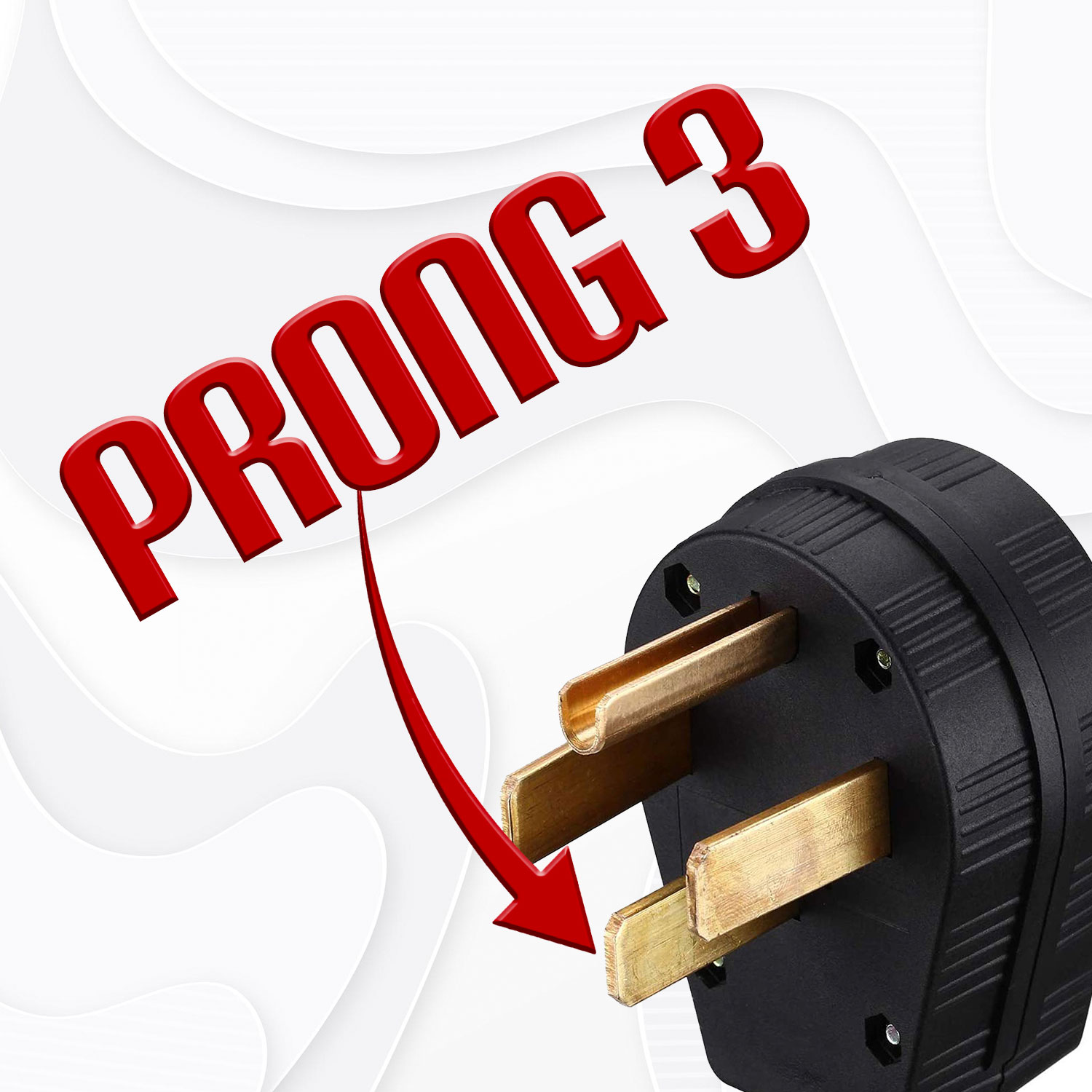
Reaction guides and MAP's (Machine Adjustment Procedures) guidelines
Listing of reaction guides for the 4 critical characteristics which may be out of spec or showing trends which are 6 to 8 points over target. Machine adjustment procedures outline the proper steps in making seam adjustments.
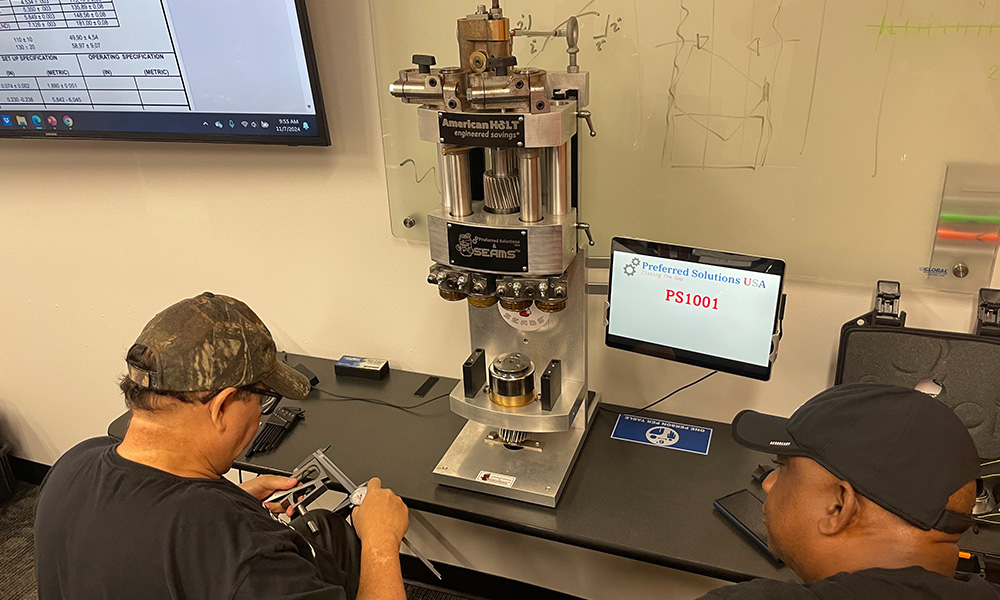
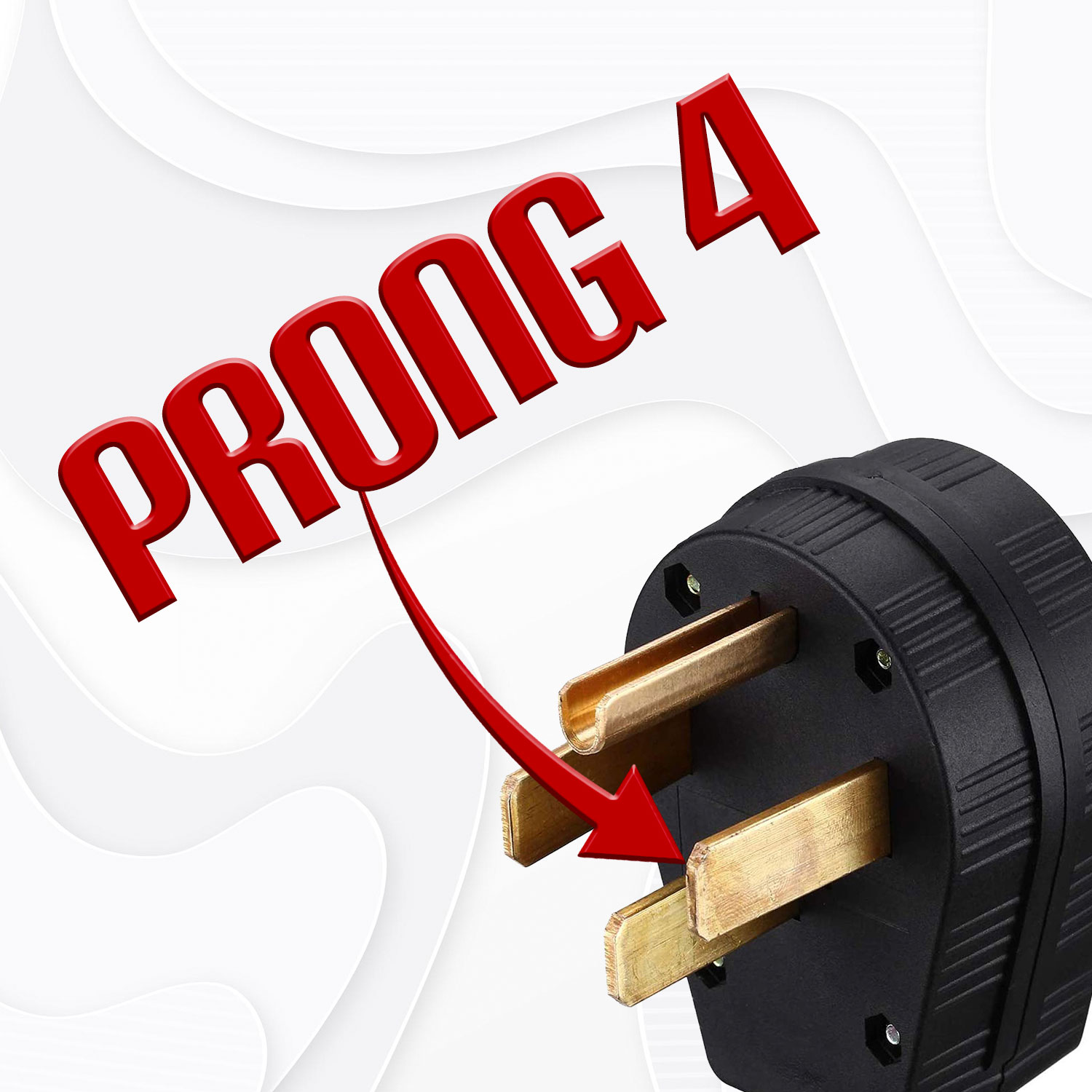
Quarterly Audits
Audits consisting of 26 major components related to seam quality with the backlash readings of feed turret, chain feed gearbox, and discharge turret. A simple 4 hour audit can detect component failure to eliminate quality and downtime issues.
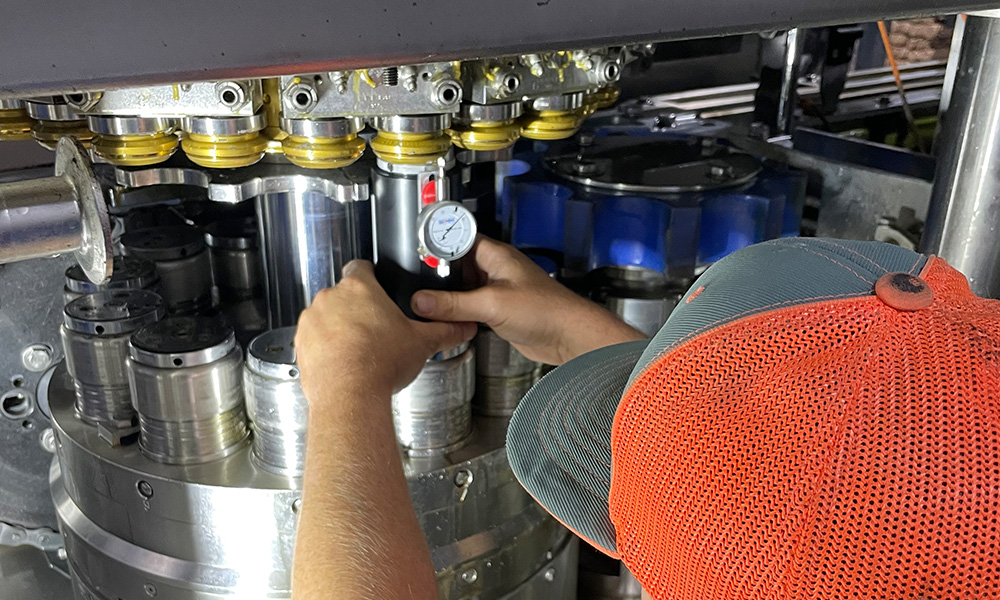